Al 2 O 3 fiber strength degradation in metal and intermetallic matrix composites
- PDF / 3,537,432 Bytes
- 15 Pages / 576 x 792 pts Page_size
- 74 Downloads / 246 Views
I. E. Locci NASA Lewis Research Center, Materials Division, 21000 Brookpark Road, Cleveland, Ohio 44135 and Department of Materials Science and Engineering, Cleveland, Ohio 44106 (Received 30 September 1993; accepted 28 January 1994)
The mechanisms for fiber damage in single crystal A12O3 fiber-reinforced composites were investigated. Both fiber fragmentation and fiber strength degradation were observed in composites with a variety of matrix compositions. Four mechanisms that may be contributing to the fiber strength loss have been proposed and include matrix reaction, reaction with binders, residual stress-induced damage, and pressure from hot pressing. The effect of matrix reaction was separated from the other three effects by sputter-coating the matrices on cleaned fibers and annealing with a temperature profile that simulates processing conditions. These experiments revealed that Y and Cr in FeCrAlY base alloys and Zr in NiAl alloys reacted with the fiber, and grooves and adherent particles were formed on the fiber surface which were responsible for the strength loss. The effects of the matrix reaction appeared to dominate over the other possible mechanisms, although evidence for reaction with binders was also found. Ridges on the fiber surface, which reflected the grain boundaries of the matrix, were also observed. In order for single-crystal A12O3 to be used as a fiber in MMC's and IMC's, a matrix or protective coating which minimizes matrix reaction during processing will be necessary. Of the matrices investigated, the Thermo-span™ alloy was the least damaging to fiber properties.
I. INTRODUCTION Metal (MMC) and intermetallic (IMC) matrix composites such as Al 2 O 3 /FeCrAlY, Al 2 O 3 /FeAl, and Al 2 O 3 /NiAl composite systems are being studied for use in advanced gas turbine engine component applications. These composite systems have been fabricated using continuous single-crystal A12O3 fiber oriented in the 0° direction and tensile tested at Proom and elevated temperatures. The results have consistently indicated that the fiber strength had been reduced during processing.1'2 Fibers were etched out of the matrix and tensile tested to assess their residual strength after fabrication. The room temperature strength of the fibers was found to be degraded by 32 to 50%. Furthermore, acoustic emission testing of Al 2 O 3 /FeAl and Al 2 O 3 /FeCrAlY during room temperature tensile testing showed the fibers had failed at low strains with calculated stresses consistent with the etched-out single fiber tensile tests.1 The loss of A12O3 fiber strength during fabrication was detrimental to the composite strength at room and elevated temperatures. In order to improve the strength of MMC's and IMC's using continuous single-crystal A12O3 fiber, the strength of the fibers must be maintained after processing. J. Mater. Res., Vol. 9, No. 6, Jun 1994 http://journals.cambridge.org
Downloaded: 04 Apr 2015
The current research focused on determining the mechanism involved in the fiber strength loss during processing. Possibl
Data Loading...
Recommend Documents

Role of Al 2 O 3 particulate reinforcements on precipitation in 2014 Al-matrix composites
186 25 3MB
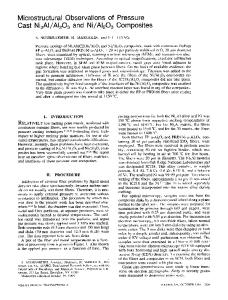
Microstructural observations of pressure cast Ni 3 Al/Al 2 O 3 and Ni/Al 2 O 3 composites
249 84 3MB